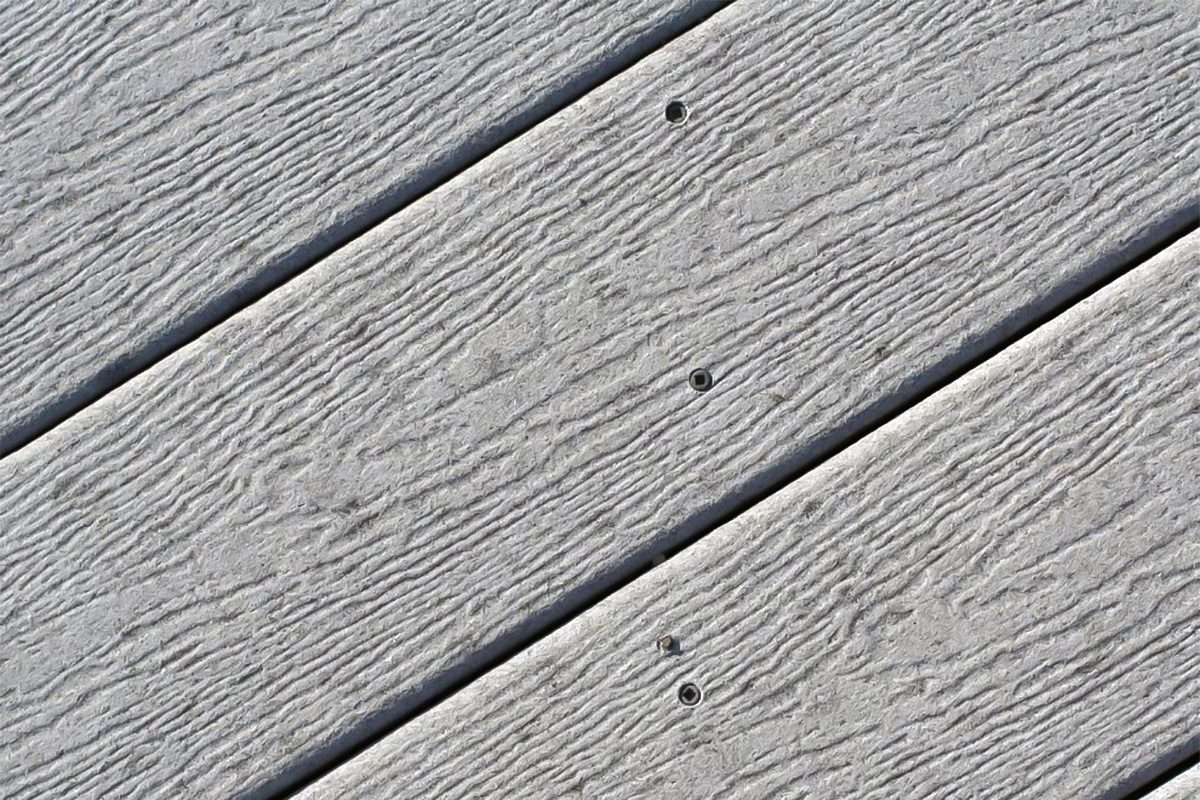
Creative Solutions To Material Shortages
Shortages of materials and delays caused by chain disruptions are motivating construction companies to search for creative substitutes for standard construction supplies. However, this has also resulted in increased costs to construction projects. It is a situation that puts building companies in the position of having to choose between upfront added costs or delayed expenses resulting from not meeting deadlines.
According to the Construction Leadership Council, shortages in material supplies, such as lumber, appliances, plywood, windows and doors, cement, and roofing tiles to name a few, have led to increase demand due to uncertainty over goods availability. These shortages have also been impacted by rising inflation and energy costs, as well as COVID’s impact on labor and production.
High Costs Versus Delays
The housing industry is perhaps one building area that is feeling the pinch the most. While the new home market is booming, record delays due to chain disruptions and material shortages have added additional costs to purchasing a home. In addition, the increase in DIY projects during COVID has contributed to the shortages. This means home buyers and home improvers must choose between waiting extensive periods of time for homes to be built or renovated or paying substantially more for new homes and home improvement materials.
Home building is not the only area of construction plagued by the inability to get supplies. All types of construction are affected, leading many companies to search for alternative building supplies, even if these materials cost more. This is, of course, not a perfect solution since those costs will be passed on to consumers, but many in the building industry feel the alternative – massive delays on construction projects – is a far more long-term costly scenario. It is a Catch-22 situation of pay more now or pay more later should projects be delayed.
But substitute materials could pan out in the long run, even if they’re more expensive now. For example, lumber prices remain higher than normal due to supply chain disruptions, leading builders to eye wood alternatives. Modular construction is one substitute since it offers speed and efficiency, and one company, MiTek, has streamlined modular construction by offering parts rather than full modules that general contractors can assemble on site in an assembly line fashion.
Alternative lumber materials are also more durable. For example, RSG 3-D’s panels, comprised of foam insulation, a steel grid and concrete covering, have been able to withstand wildfires in northern California. This alternative material is one that can actually lower the rising costs of building homes and other types of construction and can combat the expenses of ever more stringent building codes because the end result is more streamlined and less risky.
Other materials experiencing shortages include bricks, blocks and roofing products, cement, paints, sealants, steel, insulation, electrical components, plastics, screws and plumbing, but increasingly there are resourceful alternatives ready to fill the gap.
Creative Swaps
Some builders are using other insulation materials to combat the challenges of obtaining difficult-to-get petroleum-derived roof insulation boards. Structural Insulated Panels (SIPs) are a form of sandwich structured composite made up of an insulating layer of rigid core that is placed between two layers of structural board.
Another substitution is fiberglass insulation rather than mineral wool that used to take a month to obtain but now has a six-to-eight month wait. However, fiberglass insulation requires more layers of drywall, which adds to the costs. Fiberglass is also being used as reinforcement, replacing traditional steel reinforcement with a strength greater – and lighter — than steel.
Sheep’s wool, an increasingly popular alternate for building insulation, is a plant-based polyurethane foam made from kelp, hemp and bamboo that can keep out moisture and heat or cold. Another natural building material that is a good insulator is straw bale, although it needs to be combined with plaster or a similar material to protect the straw.
Reclaimed wood is good for the environment since it means less trees are cut down, and can be used for flooring, fencing, doors and window frames, cabinets, and furnishings such as table and chairs. Bamboo is an environmentally friendly substitute that can also tackle the lumber shortage. It is stronger and more flexible than lumber and grows faster than trees – in fact, it is the fastest growing plant in the world. Another tree product that can be swapped with lumber is cork, which is flexible, strong and resilient. It is also resistant to moisture, absorbs sound, and can replace lumber in flooring or in subflooring.
Reclaimed metal materials can tackle the metal shortage for use in plumbing or electrical wiring. Prefabrication concrete is another alternative created in a factory and shipped to the construction site, rather than poured on site. Bar joists are also in short supply, so concrete planks are being used by some builders because they are also easier to get, albeit more expensive.
Steel is a building product that has always been recyclable when melted as scrap steel and can be used for structural beams. According to the Steel Recycling Institute, between 60 to 80 million tons of scrap steel are recycled each year.
Along these same lines, Ferrock is a product that uses recycled steel dust to create concrete-like material. In fact, Ferrock is stronger than concrete, and absorbs more carbon dioxide than it creates.
Sawdust and wood chips are building material alternatives that when added to a cement mixture create a product that is lighter than concrete blocks or slabs. This can also cut down on transportation costs and is environmentally friendly because the parts of wood that are traditionally wasted now can be used in a productive manner. An alternative to this is hempcrete, made from the hemp plant, which is also lighter than concrete. And Mycelium, the vegetative fungus, can be used as bricks when combined with organic waste, and is resistant to water, mold and fire.
Grasscrete is an alternative building material for walkways and driveways. It has a cutout pattern, so grass grows in the cutout which permits the area’s ability to absorb water and allow for plant life to grow on the property. Papercrete, on the other hand, uses a combination of paper and other materials to create concrete-like material from recycled materials. But while papercrete can be used as plaster or to create bricks, it will wear away over time.
Other Innovative Solutions
While modular and prefab buildings have already gained in popularity over the past several years, the shortages of building materials make these an increasingly attractive alternative. For one thing, modular and prefab construction can save time and labor cement costs thanks to their factory building process compared to traditional onsite construction. They are produced in climate-controlled environments, which protect the structures and processes from the weather, thus negating replacement costs, and are more efficient when it comes to gauging needs and creating less waste which is good for the environment. And since most modular and prefab projects are completed in about a third of the time of traditional construction building, they also save on costs.
Similarly, precast foundation walls that replace laying block or pouring concrete are also made in factory settings and shipped to construction sites, reducing installation time and labor costs. One type of precast foundation walls is made of rigid foam insulation that is sandwiched between concrete and then finished by taping the joints and painting the walls. Another type of precast foundation wall is made from combining high strength concrete and insulation into a single panel that has a cavity inside for wiring, plumbing and additional insulation. An ICF Wall System is an example of a lightweight concrete material with built-in insulation and a self-anchoring stay-in-place system that saves money during and after construction. It is also fire-resistant, disaster resistant and pest resistant, energy efficient, low maintenance and durable, and promises easy and fast installation.
The Future of Construction
COVID-19 has revealed the vulnerability of construction supply chains, and no end is in sight for shortages. But newer materials can fill in the gaps. As these substitutions evolve and improve, many are and will be more efficient and sustainable, and outperform more traditional materials.
While many of these substitution materials can be currently costly, over time, demand for alternatives may diminish their added expense. And since most are more environmentally friendly and easier to install, these newer materials can help construction companies stay on track with project schedules, saving money and time in the long run.